Welding on the Water: What the US Navy Taught Me
Before attending Wesleyan university I was a welder in the U.S Navy. During my time in the Navy, I gained valuable opportunities to develop leadership abilities. I worked in quality assurance and maintenance, which taught me about accuracy, accountability, and leadership in stressful environments. For example, I conducted 15 quality assurance spot checks on life-saving equipment, which show me the importance of attention to detail. Spot checks are a random or unannounced inspection or evaluation conducted by employers or the military to ensure compliance with rules, regulations, standards, or policies. It involves checking specific aspects of an individual’s work, conduct, or adherence to guidelines.
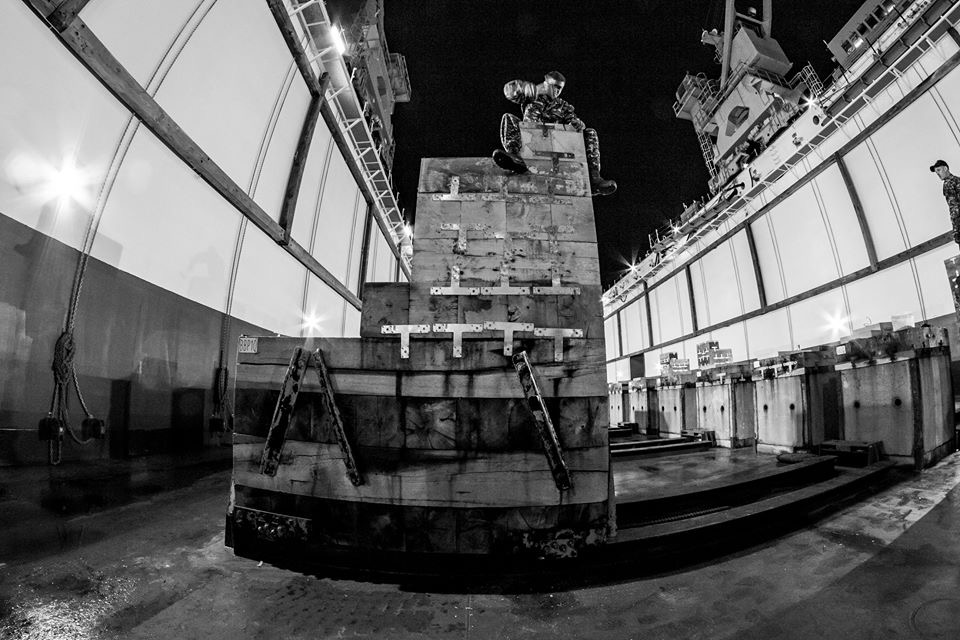
As the repair department’s Repair Petty Officer, a person who ensures the compliance of management policies and programs, and the adherence to specific guidelines I improved my leadership skills. I was responsible for the accurate accountability of 100 tools and maintenance parts, ensuring the work centers had the necessary tools to maintain equipment. Also, I performed 30 periodic maintenance system inspections, extending the life of important equipment. From this I learned the importance of preventative care not only for equipment but for people and projects, for long-term operational readiness.
A major accomplishment was reforming the Gage Calibration Program, where I managed TMDE ( Test Measurement and Diagnostic Equipment) across five work centers. All new materials and equipment were inspected to make sure they were undamaged and correctly ordered. I had to record every status, usage history, and any upcoming maintenance for the materials and equipment. By improving tracking and calibration operations, I improved our production readiness from 50% to 96%. This experience taught me the importance of micro changes on a macro level. I had to maintain detailed records of all controlled materials and TMDE. This required routine inventory audits to ensure proper accountability.
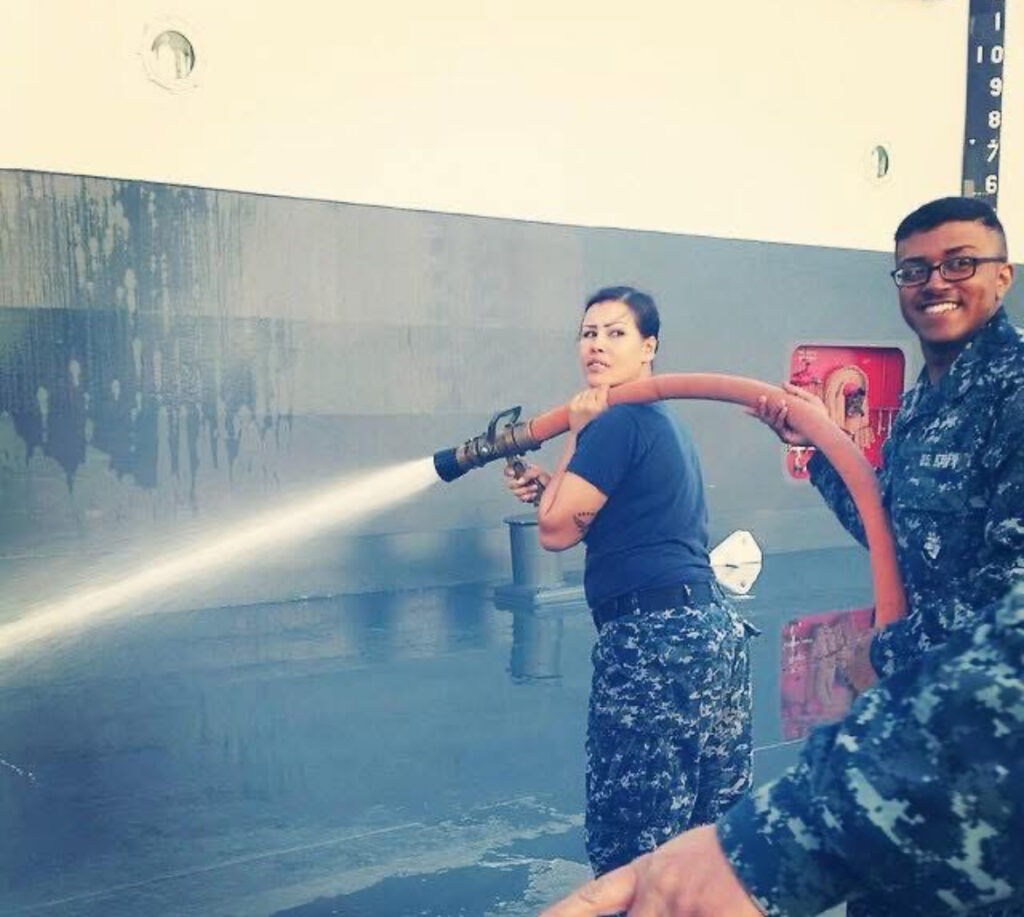
With 5 different work centers, I managed requests for parts from them, ensuring the right materials were given for the right jobs. I dealt with the calibration schedules for all testing equipment, ensuring that no work center experienced delays due to unavailable or broken equipment.
Additionally, at the same time I was the Divisional Controlled Material Petty Officer (In charge of maintaining and accounting for nuclear and radioactive level material). I handled 31 receipt inspections and maintained control of 70 nuclear-level material items, ensuring correct compliance of transfer of materials during critical submarine repairs. By better organizing the Controlled Material Petty Officer record log, I improved the inspection and issuance of materials, supporting 11 critical repairs to forward deployed submarines.